Table of Contents
- 3-RPSR parallel mechanism type pipe bender and pipe feeding mechanism
- Parallel mechanism with good motion characteristics
- Vacuum-compatible, dust-free robot using elastic hinges
- Calibration method
- Casting Mmnipulator
1. 3-RPSR parallel mechanism type pipe bender and pipe feeding mechanism
In order to develop a pipe bender that can bend pipes with arbitrary cross-sectional shapes into complex three-dimensional shapes and can handle high-mix, low-volume production, we developed a 3-RPSR (rotating [Rebolute]) with three stationary nodes and three output nodes. We are developing a device that uses parallel mechanisms connected by a kinetic chain (Prismatic – Spherical – Revolute).
It has been demonstrated that the developed device has properties suitable for pipe bending, such as “the output node can rotate infinitely around the pipe feed axis,” “high rigidity,” and “capable of realizing large attitude angle changes.”
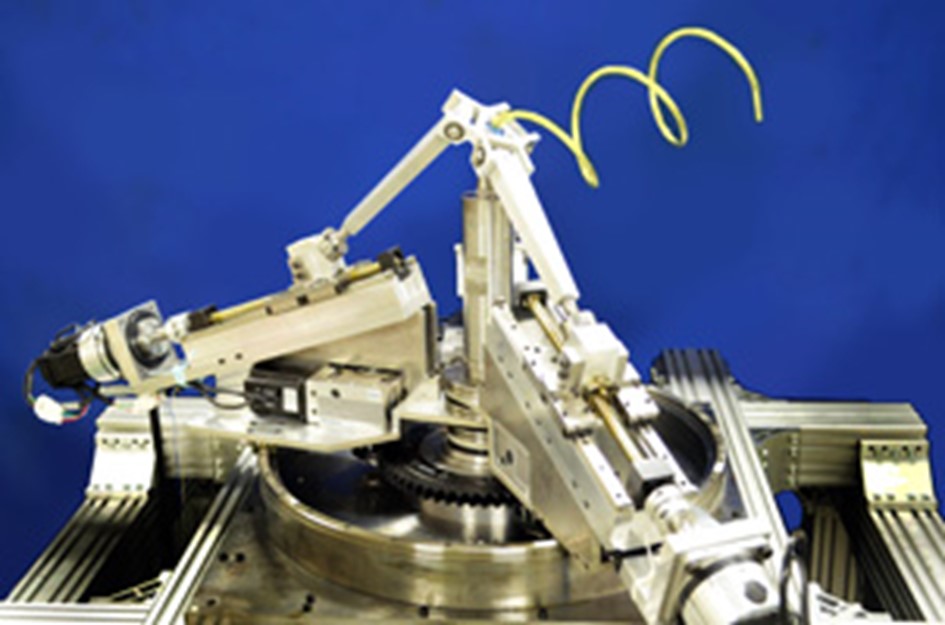
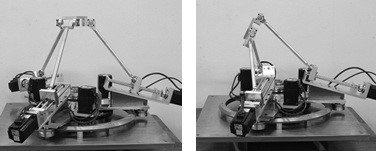
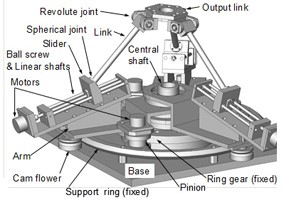
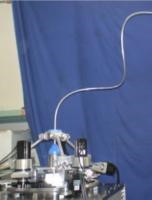
Literature (pipe bender):
- Yukio Takeda, Xiao Xiao, Kazuya Hirose, Yoshiki Yoshida, Ken Ichiryu, Kinematic analysis and design of 3-RPSR parallel mechanism with triple revolute joints on the base, International Journal of Automation Technology, Vol. 4, No. 4, 2010, pp. 346-354.
- Yukio Takeda, Sho Shou, Kazuya Hirose, Yoshiki Koda, Ken Ichiyanagi, 3-RPSR type 6-degree-of-freedom spatial parallel mechanism with triple rotating couple on a stationary node, Proceedings of the Japan Society of Mechanical Engineers Robotics and Mechatronics Conference 2010, 1A2-G20.
Literature (pipe gripping/feeding device):
- Masaru Higuchi, Rie ISHII and Yukio TAKEDA: Development of a large force gripping mechanism for a three-dimensional pipe bending machine, Japan Society of Mechanical Engineers/Robotics Mechatronics Conference 2009 Proceedings, 2A2 -A17.
- Satoshi Inada, Masaru Higuchi, Yukio Takeda, Ken Ichiyanagi, Development of a large-force gripping mechanism for a three-dimensional pipe bending machine (proposal of a gripping mechanism for pipes bent into a two-dimensional shape with a large curvature), Nippon Kikai. Academic Conference [No.10-10] Proceedings of the 10th Elemental Lubrication Design Division Conference, 2010-4-19-20, Niigata, pp.177-180.
2.Parallel mechanism with good motion characteristics
Computer control technology has developed rapidly in recent years, but unless the motion characteristics of the mechanism being controlled are excellent, it is not possible to fully enjoy its benefits. In our laboratory, we develop various types of robot mechanisms with excellent practicality such as high precision, large output displacement range, input freedom, etc., as well as their motion control methods and calibration methods, and develop processing machines and welfare equipment. It is useful for
(1) Translational parallel mechanism
3-RUU type mechanism
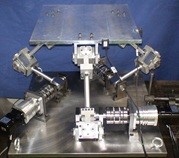
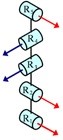
3-RRRRR形機構
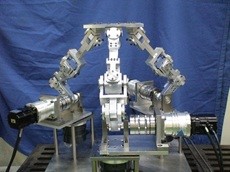
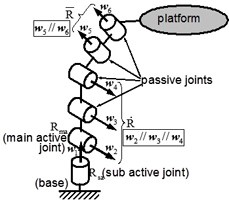
Literature:
- Syamsul Huda and Yukio Takeda, Mobility and Workspace of a 3-5R Translational Parallel Mechanism, Proceedings of IDETC/CIE 2006 ASME 2006 International Design Engineering Technical Conferences & Computers and Information in Engineering Conference, September 10-13, 2006, Philadelphia, Pennsylvania, USA., in CD-ROM, DETC2006-99340.
- Masataka Tanabe, Yukio Takeda and Syamsul Huda, Utility workspace of 3-5R translational parallel mechanism, Journal of Advanced Mechanical Design, Systems, and Manufacturing, Vol. 2, No. 6, 2008, pp. 998-1010.
- Masataka Tanabe and Yukio Takeda: Translational parallel manipulator with posture compensation, Transactions of the Japan Society of Mechanical Engineers C, Vol. 76, No. 763 (2010-3), pp. 727-733.
- Masaki Omata, Yukio Takeda, Yunho Tsoi, Peg-in-hole work experiment using a position/posture separated parallel manipulator using an impedance control system, Lecture at the 10th Elemental Lubrication Design Division Lecture, Japan Society of Mechanical Engineers [No.10-10] Collected papers, 2010-4-19-20, Niigata, pp.181-182.
(2) Rotating parallel mechanism
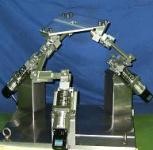
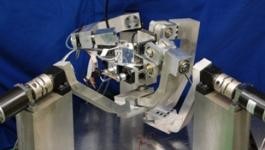
Literature:
- Syamsul Huda and Yukio Takeda, Kinematic Analysis and Synthesis of a 3-URU Pure Rotational Parallel Mechanism with Respect to Singularity and Workspace, Journal of Advanced Mechanical Design, Systems, and Manufacturing, Vol. 1, No. 1, 2007, pp. 81-92.
- Syamsul Huda and Yukio Takeda, Kinematic design of 3-URU pure rotational parallel mechanism to minimize uncompensatable error, Proceedings of the seventeenth CISM-IFToMM Symposium on ROMANSY 17, Robot Design, Dynamics, and Control, Edited by A. Tananishi, Y. Nakamura and B. Heimann, July 5-9, 2008, Tokyo, Japan, pp.443-450.
- Syamsul HUDA and Yukio TAKEDA, Kinematic Design of 3-URU Pure Rotational Parallel Mechanism with Consideration of Uncompensatable Error, Journal of Advanced Mechanical Design, Systems, and Manufacturing, Vol. 2, No. 5, 2008, pp. 874-886.
- Syamsul Huda, Yukio Takeda and Shuta Hanagasaki, Kinematic design of 3-URU pure rotational parallel mechanism to perform precise motion within a large workspace, Proceedings of the second international workshop on fundamental issues and future research directions for parallel mechanisms and manipulators, September 21-22, Montpellier, France, 2008, pp. 49-56.
- Gieseppe Carbone, Yukio Takeda, Marco Ceccarelli, Syamsul Huda, Error and Stiffness Analysis of 3-URU Pure Rotational Parallel Mechanism, Proceedings of the ISRM2009, 1. International Symposium on Robotics and Mechatronics, 2009, pp. 67-72, 2009.9.21-23, Hanoi, Vietnam.
- Syamsul Huda, Yukio Takeda and Shuta Hanagasaki, Kinematic design of 3-URU pure rotational parallel mechanism to perform precise motion within a large workspace, Meccanica, Vol. 46, 2011, pp. 89-100(DOI 10.1007/s11012-010-9400-2).
- Soichiro Matsuda, Yukio Takeda, Masaru Higuchi: Development of a 3-URU three-degree-of-freedom rotating parallel mechanism equipped with an error compensation device, 15th Japan IFToMM Conference Symposium Preprint, pp.1-8.
- Jun Okamura, Shuta Hanagasaki, Yukio Takeda: Synthesis of 2-degree-of-freedom rotating parallel mechanism with error detection and compensation functions, Japan IFToMM Conference Symposium Preprint (16th), 2010, pp.29-36.
- Jun Okamura, Shuta Hanagasaki, Yukio Takeda, Synthesis of a high-precision 2-degree-of-freedom rotating parallel mechanism without elements that directly support the output rotation center, Proceedings of the 16th Robotics Symposia, March 14, 2011. ~15th, Kagoshima, 2011, pp. 283-290.
(3) Parallel coarse/fine drive type hybrid parallel manipulator
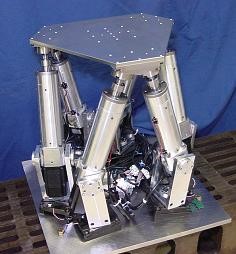
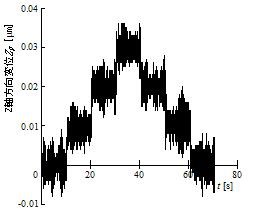
Specification:
- Decomposition energy: 10nm, 0.2μrad
- Stroke: 80×80×40mm, 20°×20°×20°
- Size: 540 x 540 x 600 mm
- Drive system: AC servo motor (coarse movement) + piezo actuator (fine movement) 6 each
Literature:
- Yukio Takeda, Kazuki Ichikawa, Hiroaki Funabashi and Kazuya Hirose, An In-Parallel Actuated Manipulator with Redundant Actuators for Gross and Fine Motions, Proc. 2003 IEEE International Conf. on Robotics and Automation, Taipei, Taiwan, September 14-19, 2003, pp.749-754, 2003.
- Yukio Takeda and Yan Guo, Improving the positioning resolution of a parallel coarse-fine drive type 6-degree-of-freedom spatial positioning mechanism, Proceedings of the 2005 Japan Society for Precision Engineering Autumn Conference, 2005.9.15-17, Kyoto, pp.1205- 1206.
- Yukio Takeda and Wei Guo, “Realization of fine positioning by a redundant parallel manipulator”, Proceedings of 2006 International Symposium on Flexible Automation, Osaka, Japan, July 10-12, 2006, pp.999-1004.
- Yukio TAKEDA, Kazuki ICHIKAWA and Wei GUO, A Spatial Six-Dof Parallel Manipulator with Redundant Actuators for Gross and Fine Motions, Journal of Advanced Mechanical Design, Systems, and Manufacturing, Vol. 4, No.2, 2010, pp.444-456.
3. Vacuum-compatible, dust-free robot using elastic hinges
Usually, ball bearings or sliding bearings are used for rotating pairs.
However, these mechanical elements have problems such as abrasion particles occurring between component parts and the necessity of lubrication, which is particularly an obstacle in applications where foreign objects enter the system and high vacuum needs to be maintained. Therefore, research on elastic hinges, which connect parts that move relative to each other with elastically deformable members and create rotational motion using the elastic deformation, has been attracting attention in recent years.
Our laboratory has proposed a double helical elastic rotation hinge, and through experimental verification using a prototype, we have confirmed that it can achieve both large rotational displacement and high load-bearing rigidity.
There are errors between the design parameters of the equipment and the actual product due to processing and assembly processes, elastic deformation of parts, etc. We are researching and developing calibration methods to detect and correct this error and achieve the desired target motion with high precision.


Literature:
- Yukio Takeda, Hiroaki Funahashi, Masashi Kimura, Kazuya Hirose: Development of a 6-degree-of-freedom spatial parallel mechanism work table using rolling spherical bearings, Transactions of the Japan Society of Mechanical Engineers, Volume 67, No. 664 (2001-12), pp.4025-4031.
- Yukio Takeda, Gang Shen, and Hiroaki Funahashi: Calibration of parallel mechanisms using Fourier series (1st report, proposal for calibration method and measurement motion selection method), Transactions of the Japan Society of Mechanical Engineers, Volume 68, No. 673 , 2002, pp.2762-2769.
- Gang Shen, Yukio Takeda, Hiroaki Funahashi: Calibration of parallel mechanisms using Fourier series (2nd report, experimental study), Transactions of the Japan Society of Mechanical Engineers C, vol. 69, no. 682, 2003, pp. 1691- 1698. (Winner of FANUC FA Robot Foundation Paper Award in 2005)
- Yukio TAKEDA, Gang SHEN and Hiroaki FUNABASHI, A DBB Based Kinematic Calibration Method for In-Parallel Actuated Mechanisms Using a Fourier Series, Transactions of the ASME, Journal of Mechanical Design, Vol. 126, September 2004, pp.856-865.
- E. Castillo-Castaneda and Yukio Takeda, Improving path accuracy of a crank-type 6-dof parallel mechanism by stiction compensation, Mechanism and Machine Theory, Vol. 43, No.1, 2008, pp.104-114.
- Junichi Imoto, Yukio Takeda, Hidenobu Saito, Ken Ichiyanagi, Optimal mechanical calibration of robots based on maximum positioning error estimation, Transactions of the Japan Society of Mechanical Engineers (ed. C), Vol. 74, No. 748 (2008), pp. 3069-3076.
- Junichi Imoto, Yukio Takeda, Hidenobu Saito and Ken Ichiryu, Optimal kinematic calibration of robots based on maximum positioning-error estimation (Theory and application to a parallel-mechanism pipe bender), Proceedings of the 5th International Workshop on Computational Kinematics, pp.133-140, Duisburg, Germany, 2009, A. Kecskemethy and A. Mueller Editors, Springer-Verlarg.
2008, pp.104-114.
Casting manipulators that project and retrieve end effectors from far away locations are thought to be effective for applications such as disaster sites and planetary exploration. In order to accurately project the end effector to a desired location and control its attitude in the air, a projection mechanism and a braking mechanism that can control the applied momentum and braking force with high precision are essential. Our laboratory is developing such mechanisms and control methods.
Literature:
- Hitoshi Arisumi, Yukio Takeda, Kazuhito Yokoi, Generation of object retrieval motion by casting manipulation, Proceedings of the Japan Society of Mechanical Engineers Robotics and Mechatronics Conference 2010, 2A2-A29.
- Asuka Shiomi, Masaru Higuchi, Hitoshi Arisumi, Yukio Takeda, Development of a wire feeding mechanism with large dynamic range tension control characteristics for casting manipulators, Proceedings of the Japan Society of Mechanical Engineers Robotics and Mechatronics Conference 2010, 2A2-B10
- Asuka SHIOMI, Masaru HIGUCHI, Yukio TAKEDA and Hitoshi ARISUMI, “Development of a Reel-out Mechanism with Large Dynamic Range Tension Control Characteristics for Casting Manipulator”, Proc. the First IFToMM Asian Conference on Mechanism and Machine Science, October 21 – 25, 2010, Taipei, Taiwan (CD-ROM proc.).