*This page contains summary public relations materials for the 2017 research grant from JKA Public Interest Incorporated Foundation “Research and development of self-propelled mesh cableway mechanism and variable structure parallel wire mechanism”.
1 Overview of the research
In this research subproject, we aim to develop basic technology for new field robot systems that are useful for work, patrol, material transportation, investigation, and rescue in natural environments and disaster sites.・A robot that self-propels in space using curved cables as a track, and a structure-variable series/parallel hybrid parallel wire mechanism that uses multiple cables and drives an end effector with multiple cables fed out from the robot. We conducted research to develop a highly reliable, high-speed, and high-output mobile robot.
2 Purpose and background of the research
Although advances in the technology of drones and rough terrain robots have been remarkable, operation in undeveloped environments such as natural environments with many obstacles or disaster sites remains difficult due to the risk of falling or getting stuck. If rails could be laid, it would be easier to pass through these environments, but the work involved in laying them would be extensive. Although there is a mechanism that allows cables to run on their own as tracks, which can be easily erected, the cables connect the two points to which they are connected with a straight line (cataliner), so they cannot be used in narrow environments with many obstacles. If we can create a self-propelled robot that installs cables in a spatial and curved manner and uses them as tracks, it would be useful for transporting supplies and patrolling in undeveloped environments such as mountains and disaster sites.
In addition, the parallel wire mechanism, which has been attracting attention in recent years, has a wide movable range and high output, so it has been proposed to be applied to disaster relief. Therefore, it is actually difficult to use it in confined environments such as natural environments with many obstacles or disaster sites. If a parallel wire mechanism with a movable range of arbitrary shape that avoids obstacles can be realized, it will be useful for investigations, rescues, and work in natural environments with many obstacles, disaster sites, etc.
Therefore, in this research, cables (called spatially-structured cableways) that are interconnected like a spider’s web and constructed spatially and curvedly (more precisely, in a polygonal manner) are used as tracks to move around the space. We conceived of a structurally variable series/parallel hybrid parallel wire mechanism that uses a self-propelled robot and multiple cables extending from the robot to drive an end effector (Figure 1). Specifically, by carrying out the research and development described below, we will develop a highly reliable, high-speed, high-output mobile robot that is useful for patrolling, transporting supplies, investigating, rescuing, and working in natural environments and disaster sites. The purpose is to develop basic technology for new field robot systems.
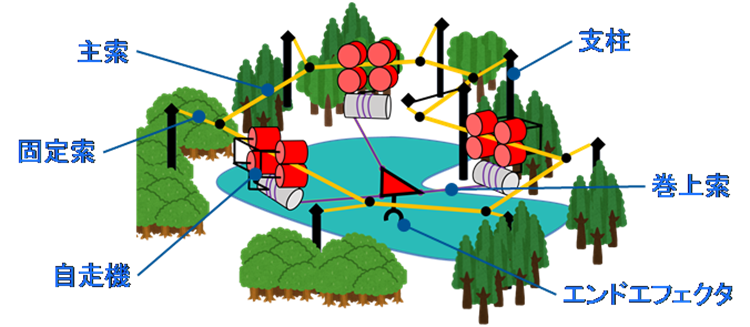
3 Research content
This research is divided into multiple research items, and the implementation details for each item are shown below.
3.1 Development of mesh cableway running mechanism
To use a network cableway as a track, it is necessary to have the ability to travel on its own beyond cable branch points. In this research item, we developed a mechanism and control method for a mobile robot that can move by itself across branch points.
First, we analyzed the functional requirements of this self-propelled cableway robot and found that the following functions are required:
(A) Ability to self-propel on a cable with knots
(B) Proceed at a branch point of the cable A function to select a direction and proceed without interfering with cables other than the direction in which the cable is traveling.Firstly,
to achieve function (A), the part that grips the cable (grip part) is equipped with a self-control device that adapts to changes in the outer diameter of the cable. Initially, we considered adopting a centering mechanism. However, further studies later revealed that it is not always necessary to position the grip part accurately in the center. Therefore, we reconsidered the functions necessary for the gripping part and found that the following functions were required:
(A-1) Function to grip and drive the main cable
(A-2) Prevent interference with the sub cable As a mechanism that satisfies these functions
, we devised a gripping section with a drive mechanism consisting of opposing pulleys with an hourglass-shaped cross section (Figure 2 (a)). This uses gravity to sandwich the cable between a pair of hourglass-shaped pulleys to increase the normal force, thereby generating a strong driving force even for cables with a low coefficient of friction. By creating semicircular gaps of the same diameter at equal intervals, it is possible to cross over the connection point with the sub cable while reliably grasping the main cable.
Next, to achieve the function (B), a mechanism is required to rotate the gripping part around the roll, pitch, and yaw axes in order to direct the gap between the pulleys of the drive mechanism toward the sub-cable at the branching point. The center of rotation in this case is the cable branch point, so a Remote-Center mechanism (RCM) is required. This can be achieved with mechanisms based on various principles, but specifically, we investigated planar mechanisms, spherical serial mechanisms, and spherical parallel mechanisms from the perspective of the movable range. As a result, we adopted the 3R spherical serial mechanism shown in Figure 2 (b) and performed detailed design. This mechanism consists of three active rotating pairs connected in series, whose rotation axes intersect at one point, and by attaching a gripping part from the self-propelled robot body through this, it can avoid sub-cables in all directions. It is now possible to run.
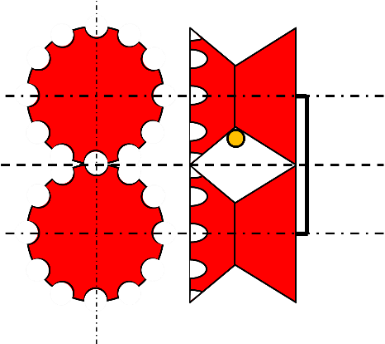
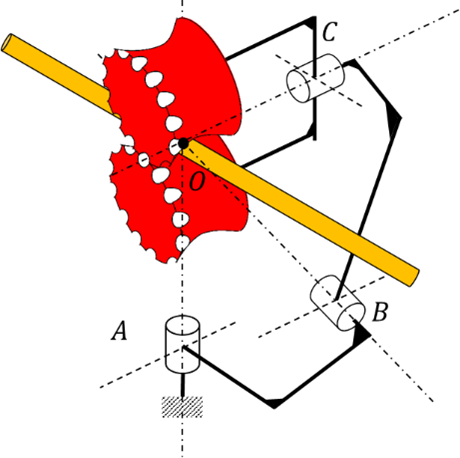
Figure 2. Structure of drive unit
We have developed the TCC78S (Tokyo Tech Cableway Crawler – No. 78 Single Arm), a single-arm reticular cableway self-propelled robot equipped with only one gripper and one RCM (Figure 3). The single arm type can be configured with only three motors including the pulley drive motor, making it inexpensive and simple.
The TCC78S can lift and lower inclined cables up to 52 degrees, enter secondary cables with up to 80 degrees of turning angle in plane, and enter secondary cables with up to 37 degrees of inclination and up to 75 degrees of turning angle. are doing.
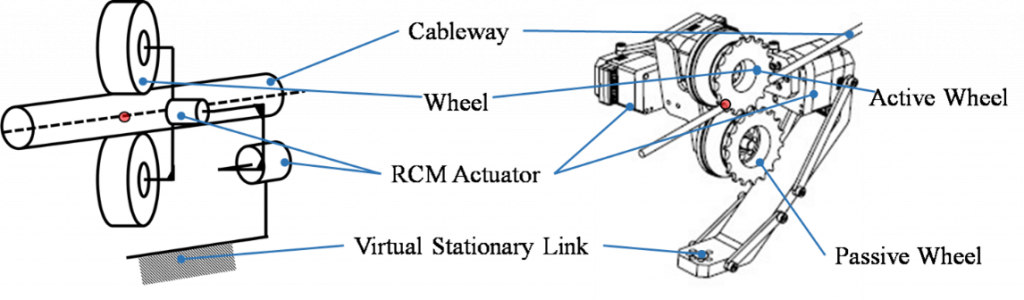
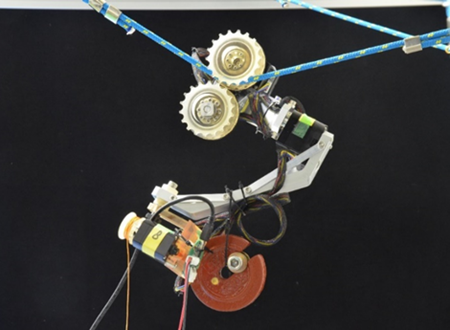
Figure 3. Single-arm reticular cableway self-propelled robot TCC78S
We also developed the TCC78D (Tokyo Tech Cableway Crawler – No. 78 Double Arm), a double-arm reticular cableway self-propelled robot equipped with this gripping part and two RCMs at the front and rear (Figure 4). The double-arm type has excellent stability because even when one side is overcoming a node, the other side can stably hold and drive the main cable.
The TCC78D can lift and lower inclined cables up to 72 degrees, enter secondary cables with a maximum turning angle of 85 degrees in plane, and enter secondary cables with a maximum slope of 48 degrees and a maximum turning angle of 63 degrees. are doing.
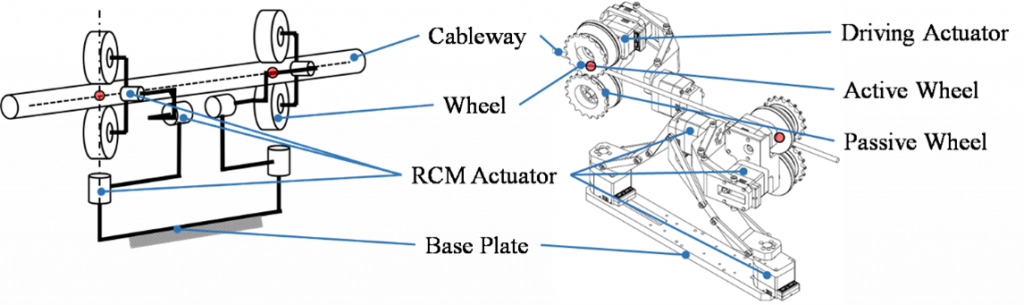
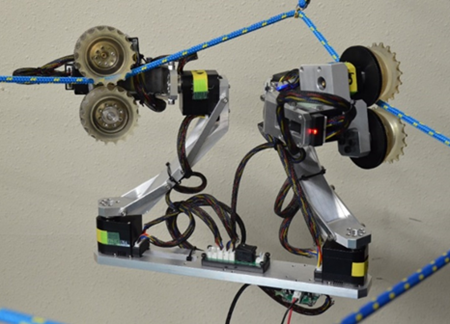
Figure 4. Double arm type cableway self-propelled robot TCC78D
3.2 Development of construction method for reticular cableway
A cableway can be set between pre-installed supports (Supporting Pillars) and branch points (Cable Knots) installed on the cables stretched between the pillars. In route generation, all of these points are set as nodes, and contact between the cable and the environment can be detected by determining the distance between the line segment connecting the nodes and the environment. These can be determined geometrically.
Regarding the presence or absence of contact between the robot and the environment while traveling on the cableway, it is necessary to consider the size of the robot itself. When generating a cableway route that can be traveled in advance, contact between the robot and the environment needs to be determined one by one, and it is common to separately determine the contact between the robot and the environment after determining the cableway route. Therefore, it is necessary to perform repeated calculations in an exploratory manner for cableways that cannot be run due to contact. In this study, we developed a method that uses the Minkowski sum to assign the robot’s size to the environment and treat the robot as a point without size when generating a cableway route. Figure 5 shows the simulation results. As shown in (a), when a robot (gray square in the figure) is on a moving cableway (yellow in the figure), consider whether it will come into contact with the environment (blue in the figure). At this time, by adding a margin for the size of the robot to the environment using the Minkowski sum, as shown in (b), the robot itself can be treated as a point. This allows the robot to be treated as a point without size, dramatically reducing the amount of calculations required when the robot is online, such as when moving.
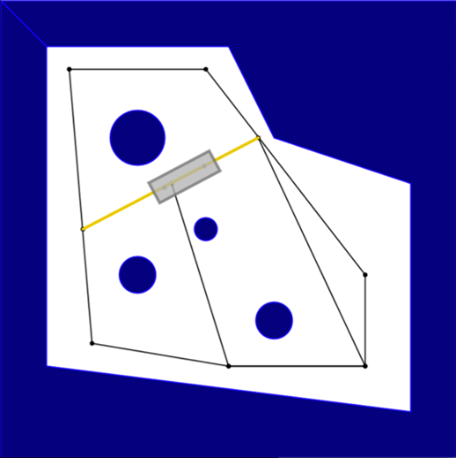
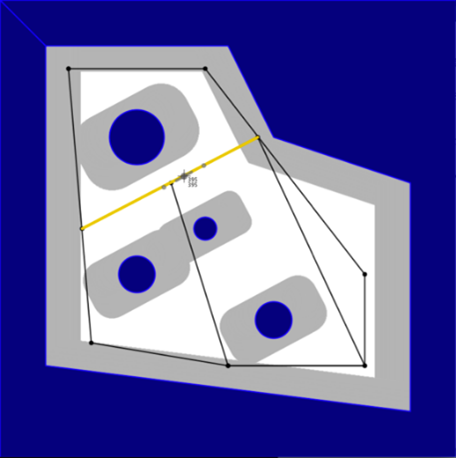
Figure 5. Transformation of handling of robot and environment by Minkowski sum
In addition, we developed a method to generate a cableway and a method to generate an efficient travel route given the environment such as obstacles. Figure 6(a) shows the environment used in the simulation with randomly placed obstacles. In this method, obstacles are treated as points. (b) shows the obstacles in the environment in (a) expressed as points. In this simulation, for simplicity, we generated the obstacle as a circle and adopted its center point as the representative point.
A cableway is laid out in an environment that includes this point cloud of obstacles. The cableway is set based on the Voronoi diagram. By using the Voronoi diagram, the cableway becomes the set of points farthest from all obstacles. In other words, the risk of the robot coming into contact with obstacles while moving can be minimized. (c) shows the Voronoi diagram applied to the environment in (b). In addition, the calculated intersection point is shown in (d). This intersection actually becomes a node and a branch point of the cable.
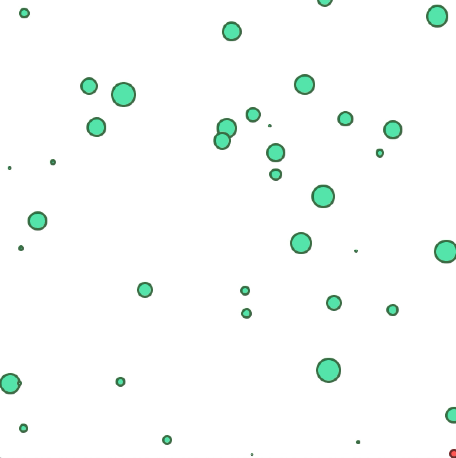
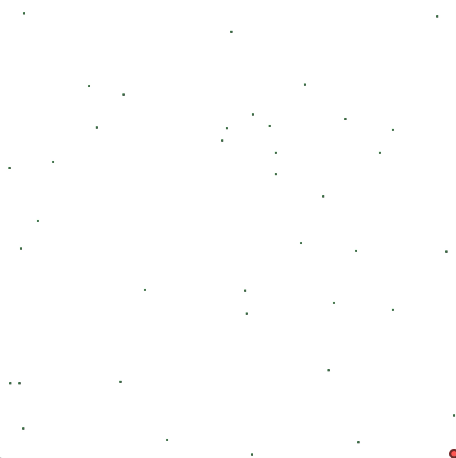
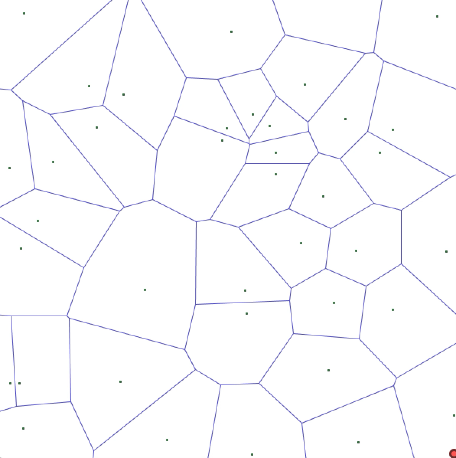
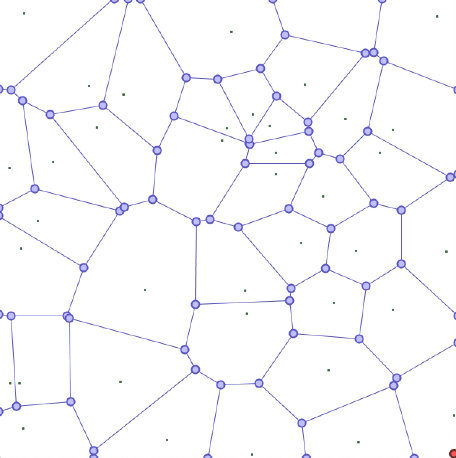
Figure 6. Generation of cableway according to the field
Set a target point on this cableway and select a cableway route that will allow you to travel efficiently to that point. Figure 7 shows the route generation step by step. First, set the target position in the target area (a). The proposed system performs tasks using a parallel wire mechanism fixed to multiple robots moving on a wire cableway. Therefore, when a target point is set at an arbitrary position, the robot’s destination is included in the closed loop structure of the cableway that includes it. In this simulation, the closest point on the cableway to the target point is set as the destination in order to set the destination within the closed loop structure of the cableway that includes the target point. After that, a straight line connecting the initial position and the destination is generated, and the node closest to the straight line is included in the route. This is repeated until all routes finally match the cableway. The process of these iterative calculations is shown from (c) to (o) in the figure. By using a straight line as a standard, the shortest distance between nodes is taken at every step, and it can be said that the cableway route with the shortest travel distance can be selected.
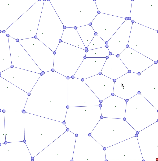
Figure 7. Generation of the shortest cableway travel route
In addition, regarding a cableway on which a robot moves, which is constructed by suspending multiple wires into a mesh, we investigated the catenary curve of the suspended wires in order to extend route searching in two dimensions to three dimensions. Specifically, we investigated through experiments the extent to which curves calculated based on a theoretical formula called catenary curves, which model the curves of wires in fields such as architecture, can actually reproduce suspended wires. The experiment used image processing technology to photograph and analyze the suspended wire, and compared the error with the curve derived from the theoretical formula. Experiments have shown that although the catenary curve has errors due to the stiffness and elasticity of the wire depending on the material, the curve derived from the theoretical formula generally agrees with the experimental results.
In the future, we will develop a model that applies catenary curves to wires that have node points on wires that are suspended from fixed points, as well as wires that have node points on those wires and which form cableways in a composite network. By using , we will build a system that estimates the three-dimensional shape formed by the cableway from node position information. We will also discuss changes in maneuvering shape due to the robot’s own weight when the robot is at an arbitrary point on the cableway.
3.3 Development of parallel wire mechanism using multiple cableway self-propelled robots
By letting out more cables from multiple cableway self-propelled robots and connecting them to the end effector, the structure variable series/parallel hybrid parallel wire mechanism has a movable range of arbitrary shape that avoids obstacles and avoids the movable range from becoming a convex polyhedron. can be configured. As an example of this concept, in this research item, we prototyped a 3-degree-of-freedom mechanism using two self-propelled robots as described in 3.1 (Figure 8).
This structure-variable hybrid wire mechanism attaches a winch to two single-arm self-propelled robots that run on a spatially structured network cableway, and uses two cables that extend from these to position the end effector. It can be performed. In this prototype, a spherical camera is mounted on the end effector, allowing the self-propelled robot to run on a mesh cableway and position it by hoisting and manipulating the cable, making it possible to realize the concept proposed in this research. We confirmed that this is the case.
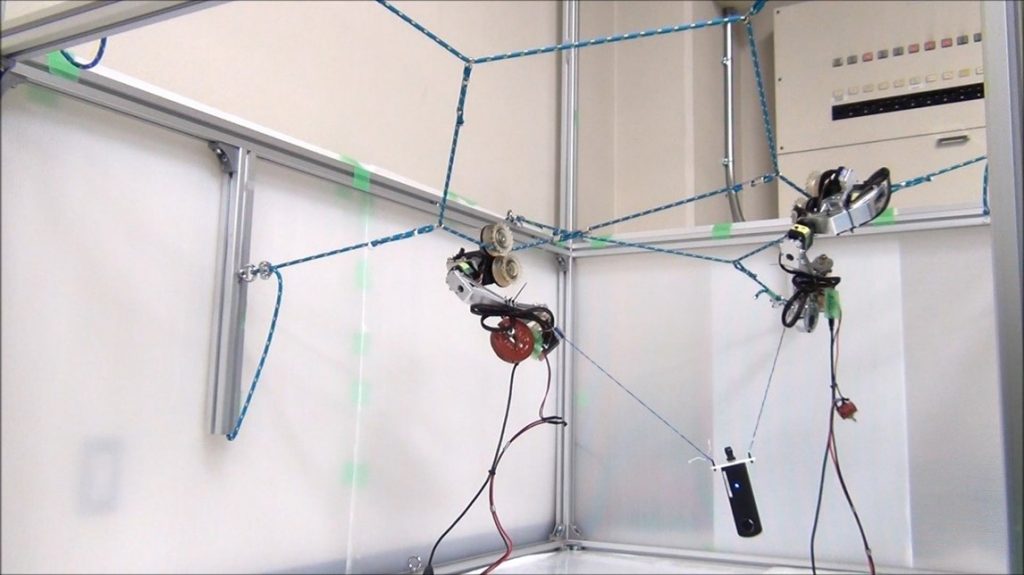
4. How this research will be utilized in the real world – Outlook
In the medium to long term, the results of this research are expected to lead to the realization of highly efficient, fast, and reliable mobile robots that are useful for continuous transportation of supplies and patrols in undeveloped environments such as mountains and disaster sites. This innovation is the realization of a high-power mobile robot that is useful for investigation, rescue, and work in natural environments with many obstacles, disaster sites, etc. These technologies can be applied to disaster response robots, decommissioning robots, decontamination robots, natural environment monitoring robots, and agricultural and forestry robots, and the results of this research are essential for the practical application of these robot systems. be.
In fact, based on the results of this research, we applied for the 2019-2020 public interest incorporated foundation JKA research grant with a research plan that further expanded the theme and included the participation of new co-researchers, and received a grant decision. This project is based on the results of this research and is planned to be refined into practical technology for automatic transportation of materials and environmental monitoring in natural environments such as mountains and forests, and further results are expected.
There are also companies that are interested in the results of this research, and we believe that we can expect early practical application.
5 Positioning of this research in the flow of teaching and research history
Yusuke Sugawara, the research representative, has made building and developing robot system design his lifework, and in this work, the “reticulated cableway self-propelled robot” and “structure-variable hybrid wire mechanism” are proposals for completely new robot systems. It is of great significance in the sense that it is done. In addition, the concept of applying a parallel wire mechanism to a self-propelled working mobile robot on an orbit is a challenge for me as a mechanism researcher, especially in the field of field robotics, which has been rapidly developing recently, such as drones and SLAM.
Co-researcher Hiroshi Endo is working on the application of robot technology with sustainability as a keyword, and this research can be applied to monitoring lakes and forests in relation to environmental sustainability. be. We are also working on research on parallel wire mechanisms focusing on the characteristics of wires and on systems using mobile robots, which are important as technological developments for the application of basic technology.
6 Intellectual property, published papers, etc. related to this research
[Intellectual property]
None (1 application in preparation)
[Papers/International conferences]
1. | Daisuke Matsuura, Taishu Ueki, Yusuke Sugahara, Minoru Yoshida and Yukio Takeda, Reproduction of Long-Period Ground Motion by Cable Driven Earthquake Simulator Based on Computed Torque Method, Proc. of the Fourth International Conference on Cable-Driven Parallel Robots, Krakow, Poland, 2019.(印刷中) |
[Domestic conference proceedings]
2. | Randy Raharja Sudiono, Yusuke Sugahara, Mitsuru Endo, Daisuke Matsuura and Yukio Takeda, Cable Traversing Robots on Spatially Structured Cableway for Reconfigurable Parallel Cable System, Japan Society of Mechanical Engineers Robotics and Mechatronics Conference 2019, Hiroshima Prefecture, June 2019. (currently printing) |
3. | Yasunobu Ueki, Daisuke Matsuura, Yusuke Sugawara, Minoru Yoshida, Yukio Takeda, Control of parallel wire seismic motion simulator using computational torque method and reproduction of long-period earthquake motion, Proceedings of the 36th Annual Conference of the Robotics Society of Japan, 2K1- 04, Aichi Prefecture, September 2018. |
4. | Sotaro Tanizawa, Mori Soraku, Atsushi Watanabe, Hiroshi Endo, Yusuke Sugawara, Nobuhiro Muto, Takao Kakizaki, Torque-adjustable high-output wire reel robot using commercially available electric reels, Japan Society of Mechanical Engineers Robotics and Mechatronics Conference 2018, Fukuoka Prefecture , 2A1-J12, June 2018. |
5. | Sotaro Tanizawa, Osamu Endo, Yusuke Sugawara, Nobuhiro Muto, Takao Kakizaki, Research on positioning using a suspended parallel wire mechanism (parallel wire experimental device with changeable over-constraint type/suspended type configuration), 18th Measurement Automatic Control Society System Integration Division Lecture (SI2017), Miyagi Prefecture, pp. 557-559, December 2017. |
6. | Mori Sagara, Osamu Endo, Yusuke Sugawara, Nobuhiro Muto, Takao Kakizaki, Research on positioning using a suspended parallel wire mechanism (determination of the state of an object by focusing on wire slack), 18th Society of Instrument and Control Engineers System Integration Division Lecture (SI2017), Miyagi Prefecture, pp. 560-563, December 2017. |
[Invited lectures, etc.]
7. | Yusuke Sugawara, Daisuke Matsuura, Yukio Takeda, Development of high-precision parallel mechanism, Kinki University Graduate School of Science and Engineering Interdisciplinary Research, Osaka Prefecture, April 2018. |
8. | Yusuke Sugawara, Daisuke Matsuura, Yukio Takeda, Development of high-precision parallel mechanism, 7th Visible and Infrared Observation Equipment Technology Workshop, Kyoto Prefecture, November 2017. |
9. | Yusuke Sugawara, Robot systems that support humans – Design, control, and integration -, Ota Industrial Promotion Association 89th Tokyo Institute of Technology Technical Seminar, Tokyo, August 2017. |
7 Deliverables related to subsidized projects
(1) Nothing created through the subsidized project
(2) Anything created under this project other than (1) Publication papers mentioned above, etc.
8. Contact for inquiries regarding business details
Affiliated institution name: Tokyo Institute of Technology
Address: 2-12-1 (i6-15) Ookayama, Meguro-ku, Tokyo 152-8552
Applicant: Associate Professor Yusuke Sugahara
Department in charge: School of Engineering, Department of Mechanical Engineering, Department of Functional Systems
E-mail: sugahara@mech.titech.ac.jp
URL: http://www.msd.mech.e.titech.ac.jp/