*This page contains summary public relations materials for the JKA Public Interest Incorporated Foundation 2019 research grant “Practical technology development of self-propelled structurally variable parallel robots on reticular cableways.”
1 Overview of the research
In this research subsidy project, we proposed a structure in which hand effectors are driven by cables that are extended from multiple self-propelled robots by interconnecting them in a network, which was proposed as a research subsidy in 2017 and 2019. Regarding variable serial/parallel hybrid wire robots, this content will be developed and expanded to include the mechanism and control method of reticular cableway self-propelled machines, cableway construction and route planning methods, material transportation technology and environmental monitoring technology using self-propelled machines, and parallel mechanisms. By conducting research and development on work techniques, etc., we conducted research to develop practical technology as a highly reliable field robot system that is useful for work, material transportation, investigation, etc. in the natural environment and disaster sites. ..
2 Purpose and background of the research
The research representatives proposed a field robot using a reticular cableway self-propelled mechanism and a structure-variable parallel wire mechanism in a 2017 research subsidy project (multi-year). This is a system that uses cables that are interconnected like a spider’s web and are laid out in a spatial and curved manner (called a reticulated cableway) as a track to run on its own in space. This is a structure-variable series/parallel hybrid parallel wire robot that drives hand effectors using multiple cables. In this project, we proposed this basic idea, developed a principle verification model of a mesh cableway running mechanism and a cableway construction method, and proceeded with research on a parallel wire mechanism using this.
This research aims to further develop and expand this content and develop practical technology for field robots. Specifically, we are developing mechanisms and control methods for self-propelled reticulated cableways, research on cableway construction and route planning methods, development of materials transportation technology, development of environmental monitoring technology, and development of work technology using parallel mechanisms. The purpose of this research was to develop practical technology for a new field robot system, which is a highly reliable, high-speed, high-output mobile robot that is useful for work, patrolling, material transportation, investigation, and rescue at disaster sites and disaster sites.
3 Research content
The plan for this research is divided into multiple research items, and the implementation details for each item are shown below.
① Development of mechanism and control method for self-propelled reticulated cableway machine
To use a network cableway as a track, it is necessary to have the ability to run on its own while passing through cable connection points (branch points). For example, in order to pass through a fork in the road, you must be able to choose between the two cableways you are going to. By the start of this research, we had achieved running on a cable and passing through branch points at branch points, but the hardware was not optimized and the control method was manual control, so automation is not possible. It was necessary to develop kinematics and motion planning methods.
Therefore, we improved the current prototype of a mobile robot that can self-propel across junctions, and developed a smaller, lighter, more reliable mechanism and a basic attitude control method.
First, we formulated the kinematics of the Remote Center Mechanism (RCM, Video 1). Next, based on this, we formulated the kinematics of a double arm type self-propelled aircraft. Based on this model, we formulated the relationship between the angular displacement of the six active joints and the posture of the drive unit, which is the end effector. By using this result, given the direction of the auxiliary rope in which it travels, it is possible to find the motion pattern of each joint to travel in that direction. Based on this, we developed a motion planning method and a mechanism optimization method.
Here, we modeled the branching point of the cable and determined the kinematics of the 3R serial spherical mechanism that the double arm type self-propelled vehicle has at the front and rear. In particular, since this mechanism cannot generate a moment around the cable axis, it is not always possible to achieve this posture even if the postures of the front and rear drive sections are given relative to the cable model, and when realizing the postures of the two given drive sections. In order to calculate the posture that a robot can take with respect to a cable, we developed a calculation method that solves a kineto-static inverse problem that takes into account static balance. Next, we used this to develop a motion planning method for passing through cables with branch points. The target joint angle is generated by calculating the posture transition of the drive unit necessary for passing the branch point and performing spherical linear interpolation using quaternions. Furthermore, using this motion planning method, we optimized the mechanical constants so that there would be no interference with the cable or singularity problems during the series of motions when traveling at a branch point. Videos 2 to 6 show the prototype TCC80D developed above passing through a cable branch point.
Video 1. Motion of the spherical mechanism of TCC80D
Video 2. Mobile robot TCC80D traversing a horizontal intersection of the structured cableway
Video 3.Mobile robot TCC80D traversing a spatial intersection of the structured cableway using “Tensioning”
Video 4.Mobile robot TCC80D traversing a spatial intersection of the structured cableway using “Tensioning”
Video 5.Mobile robot TCC80D traversing a spatial intersection of the structured cableway using “Tensioning”
Video 6. Mobile robot TCC80D traversing a spatially structured cableway
② Research on cableway construction and route planning methods
Since mesh cableways are connected to each other and constructed in a polygonal manner in space, the arrangement of other cables (auxiliary cables) to achieve the target shape of a certain cableway (main cable) is derived mechanically. be able to. Also, at this time, it is necessary to find a path for the cableway that does not interfere with the environment.
Based on the model of the work to be performed and the environment model, we developed a cable placement method that would prevent the robot body and cables from interfering with the environment. Specifically, we researched a cableway route planning method based on RRT* and Voronoi diagrams, and developed a sub-cable planning method that takes into account dynamic balance.
[ Cableway route planning method based on RRT* ]
We generate multiple main cable routes from the start point to near the goal point, with the condition that the self-propelled aircraft can travel on its own throughout the entire distance without interference with obstacles, and select the route with the shortest total distance from among them. I created an algorithm to derive it.
The method is based on RRT*, and by determining collisions with obstacles taking into account the size of the self-propelled aircraft, and determining edges taking into account the maximum tilt angle and maximum turning angle that the self-propelled aircraft can run, This method generates multiple routes from the start point to the goal point that allow the aircraft to travel the entire distance on its own without interfering with obstacles, and then derives the shortest route from among them.
[Cableway route planning method based on Voronoi diagram]
What was previously studied in a simulated environment, targeting a two-dimensional plane, has been extended with the intention of applying it to a real environment. First, we obtain three-dimensional point cloud data of obstacles in the real environment measured using cameras, LiDAR, etc. This is converted and used as voxel data (Figure 1). A three-dimensional Voronoi diagram is generated based on this voxel data, taking into account contact with the robot, and cableways and routes are created from Voronoi lines and Voronoi points.
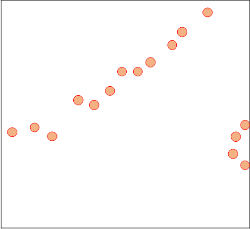
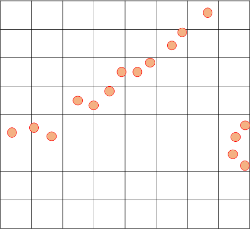
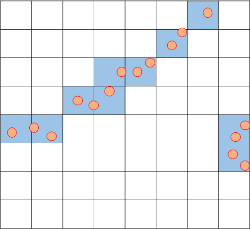
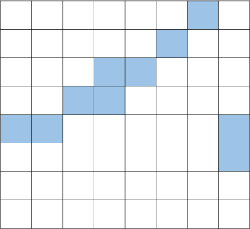
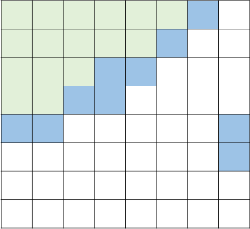
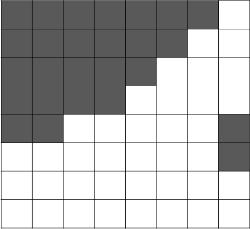
Figure 1. Obstacle location extraction method based on environmental measurement information
[Sub-route planning method considering mechanical balance]
We researched a method for generating sub-cableways in three-dimensional space. Four or more wires are required to constrain the three degrees of freedom of the position of the node in space. In addition to the two wires that form the cableway at the node, two or more wires that form the sub-cableway are required. In this study, there are two auxiliary cableways, and the direction of the first cableway is determined so that the holding force at the node point is maximized, and the direction of the second cableway is determined so that the tension on the cableway and the auxiliary cableway is evenly distributed. We implemented this as an algorithm that can be automatically calculated. Figure 2 shows the generated application example.
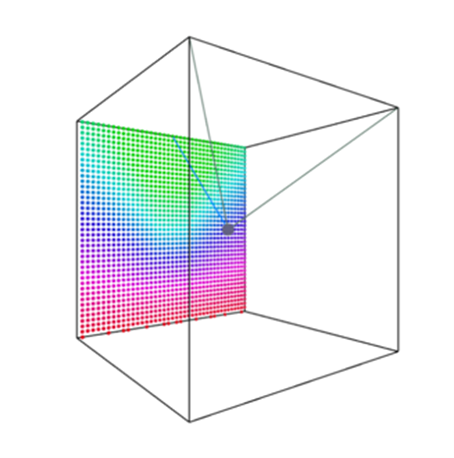
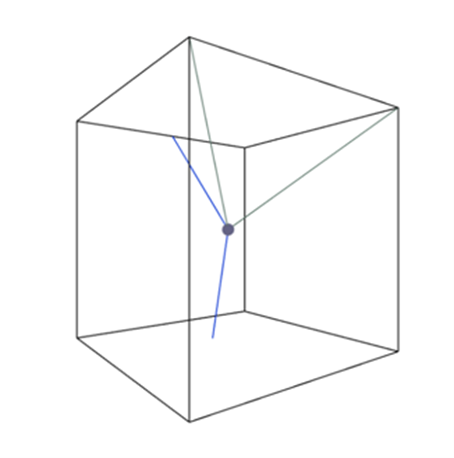
Figure 2. Generation of sub-cableway
[Research on cableway construction methods (research on throwing robots)]
We devised a method that allows the robot itself to construct cableways and sub-cableways, and constructed a cable model for this purpose. Figure 3 shows the construction method used in this study. Rather than throwing an object, the cable itself is thrown using a flexible structure mounted on the robot. Hang the cable around the existing cableway or object (such as a tree branch) that you want to construct, and then fix the hook-shaped structure at the tip by pulling the cable around by hand. To realize this cable throwing, we modeled the throwing mechanism and cable as a rigid multi-link model shown in Figure 4, and confirmed the validity of the model through basic experiments.
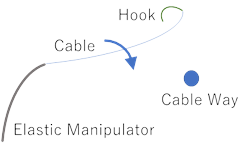
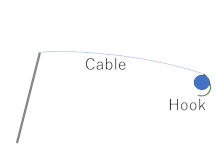
Figure 3. Erection of cableway and sub-cableway by throwing wire
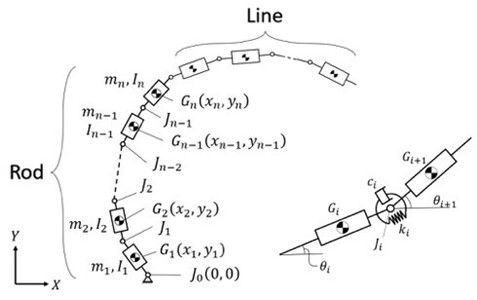
③Development of materials transportation and environmental monitoring technology
We worked on developing a small robot that works in conjunction with a self-propelled reticular cableway to transport goods and monitor the environment.
This robot is equipped with a winding mechanism that moves from a self-propelled machine on a mesh cableway built at a certain height above the ground to the ground to avoid the bamboo and shrubs that cover the forest floor. By descending with a tether, it can observe near the ground surface and place small animal traps and sensors on the ground surface. In this research, we developed an active flipper to avoid obstacles such as branches and rocks during descent, a flywheel to suppress the rotation around the tether that occurs when the flipper is driven, and a flywheel to suppress the rotation around the tether that occurs when the flipper is driven. We developed a mechanism for mitigating the shock caused by a collision, as well as elemental technology for its control system. We also developed prototypes for each elemental technology. As an example, Video 7 shows a prototype equipped with an active flipper, and Figure 5 shows a prototype equipped with a flywheel to suppress rotation around the tether. This aircraft is equipped with a power supply, control circuit, and wireless communication device, and can operate autonomously by remote control.
Through experiments, we confirmed that each of the prototypes we developed had performance that could withstand use in forests.
Video 7. Lowering robot with active flippers
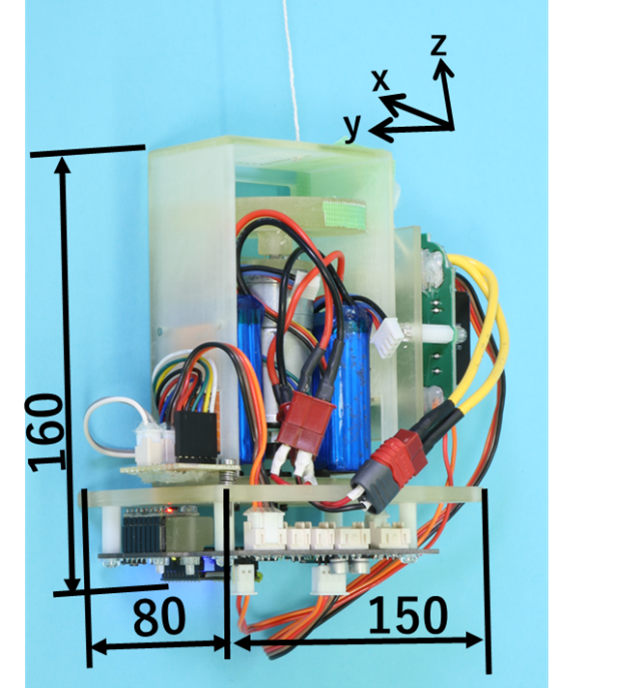
④ Development of work technology using hybrid wire robots
As an example of the structure-variable series/parallel hybrid wire mechanism that can change the range of motion proposed in this study, we prototyped a 3-degree-of-freedom mechanism using two of the developed reticular cableway self-propelled machines.
Video 8 shows the operation experiment of the developed structurally variable series/parallel hybrid wire mechanism. This is a system in which winches are attached to two double-arm TCC80D self-propelled cableway machines that run on a spatially constructed reticulated cableway, and the end effector is positioned using two wires that are fed out from these.
In this experiment, a mesh cableway is constructed to surround an obstacle. In such an environment, a normal suspended parallel wire mechanism requires an end effector to be placed around the obstacle due to interference between the wire and the obstacle. Although positioning is difficult, the proposed system is able to construct a suspended parallel wire mechanism in which the self-propelled machine moves to avoid obstacles and the wires do not interfere with obstacles.
https://www.youtube.com/embed/3_8I3GaJSlg?feature=oembedVideo 8. Structure-variable hybrid parallel wire robot configuration and camera positioning experiment
4. How this research will be utilized in the real world – Outlook
In the medium to long term, the results of this research are expected to lead to the realization of highly efficient, fast, and reliable mobile robots that are useful for continuous transportation of supplies and patrols in undeveloped environments such as mountains and disaster sites. This innovation is the realization of a high-power mobile robot that is useful for investigation, rescue, and work in natural environments with many obstacles, disaster sites, etc. These technologies can be applied to disaster response robots, decommissioning robots, decontamination robots, natural environment monitoring robots, and agricultural and forestry robots, and the results of this research are essential for the practical application of these robot systems. be.
Furthermore, based on the results of this research, we have applied for a research grant from JKA, a public interest incorporated foundation, for the 2021-2022 academic year with a research plan that further expands the theme and includes the participation of new co-researchers, and has been approved for grant funding. Based on the results of this research, this system consists of a self-propelled reticular cableway robot, a throwing robot that constructs a cableway in the environment by throwing cables, and a thrown robot that is thrown while towing the cable. It is a field robot system that can automatically construct a network cableway in a maintenance environment, run on it by itself, and position itself below the cableway by descending from there, and further results are expected.
There are also companies that are interested in the results of this research, and we believe that we can expect early practical application.
5 Positioning of this research in the flow of teaching and research history
Yusuke Sugawara, the principal investigator, has made it his life’s work to build and develop robot system design, and among these, the “reticular cableway self-propelled robot” and “structure-variable hybrid wire mechanism” are proposals for completely new robot systems. This is of great significance in the sense that it is carried out. In addition, the concept of applying a parallel wire mechanism to a self-propelled working mobile robot on an orbit is a challenge for me as a mechanism researcher, especially in the field of field robotics, which has been rapidly developing recently, such as drones and SLAM.
Co-researcher Hiroshi Endo has been working on the application of robot technology with sustainability as a keyword in his past research, and this research, which can be applied to monitoring lakes and forests, is positioned in that direction. ..We are also working on research on parallel wire mechanisms focusing on the characteristics of wires and on systems using mobile robots, which are important as applied research for these basic technologies.
Co-researcher Hiroyuki Ishii is working on the development of robot technology that coexists with nature and living things, and in recent years has particularly focused on developing robots for observing and preserving wild animals and plants in forests. The reticular cableway self-propelled robot being developed in this research is extremely promising as a new movement technology in forests, and is also expected to collaborate with the environmental monitoring robots that have been developed so far, making it possible to use robots to monitor forests. It is positioned as an important and rapidly accelerating research.
6 Intellectual property, published papers, etc. related to this research
[Paper/International conference (peer-reviewed)]
1. | Hirotsugu Kano, Yusuke Sugawara, Osamu Endo, Hiroyuki Ishii, Yukio Takeda, Research on robots that run by themselves on a net-like cableway constructed structurally in space (on double-arm kinematics, motion planning, and mechanism optimization) ), Journal of the Robotics Society of Japan, volume and number to be determined, pages to be determined, 2021. (Accepted, currently being printed) |
2. | Andres Osorio Salazar, Yusuke Sugahara, Daisuke Matsuura, Yukio Takeda, Scalable Output Linear Actuators, a Novel Design Concept Using Shape Memory Alloy Wires Driven by Fluid Temperature, Machines, Vol. 9, Issue 1, 14, 2021. |
3. | Yusuke Sugahara, Guangcan Chen, Nanato Atsumi, Daisuke Matsuura, Yukio Takeda, Ryo Mizutani and Ryuta Katamura, A Suspended Cable-Driven Parallel Robot for Human-Cooperative Object Transportation, In: Venture G., Solis J., Takeda Y., Konno A. (eds), ROMANSY 23 – The 23rd CISM-IFToMM Symposium on Robot Design, Dynamics and Control (ROMANSY2020), pp. 109-117, Springer, Cham, 2020. |
4. | Andres Osorio Salazar, Yusuke Sugahara, Daisuke Matsuura, and Yukio Takeda, A Novel, Scalable Shape Memory Alloy Actuator Controlled by Fluid Temperature, In: Niola V., Gasparetto A. (eds), Advances in Italian Mechanism Science, The 3rd International Conference of IFToMM ITALY, pp. 617-625, Springer, Cham, 2020. |
[Domestic conference proceedings]
5. | Ryonori Hakamada, Osamu Endo, Yusuke Sugawara, Hiroyuki Ishii, Yukio Takeda, Research on casting using a small low-power manipulator applying fly fishing principles (1st report: Modeling of line taking into account payout from the rod), Japan Japan Society of Mechanical Engineers Robotics and Mechatronics Lecture (ROBOMECH2021), 2P3-H15, 2021. (currently printing) |
6. | Hirotsugu Kano, Yusuke Sugawara, Osamu Endo, Hiroyuki Ishii, Yukio Takeda, Research on robots that run by themselves on a net-like cableway built structurally in space (on double-arm kinematics, motion planning, and mechanism optimization) ), Proceedings of the 38th Academic Conference of the Robotics Society of Japan, 3C1-04, 2020. |
7. | Keita Noda, Wataru Matsuhiro, Nu Nuwin, Shigehide Suzuki, Junichi Haruyama, Yusuke Sugawara, Atsuo Takanishi, Hiroyuki Ishii, Production of a small robot that performs posture control and exploration of vertical hole walls, 38th Robotics Society of Japan Academic Conference Lecture, 2F1-07, 2020. |
8. | Hiroshi Endo, Daiya Ichikawa, Yusuke Sugawara, Hiroyuki Ishii, Self-propelled structurally variable parallel robot with mesh cableway – Method for generating mesh cableway -, 37th Academic Conference of the Robotics Society of Japan, 1H1-05, 2019. |
[Invited lectures, etc.]
9. | Yusuke Sugawara, Driving robots using differential mechanisms, Japan Society of Mechanical Engineers Research Cooperation Project Committee RC283 “Testing and Survey Research Subcommittee for Innovative Technologies Related to Design, Manufacturing, and Evaluation of Gear Devices” 3rd General Subcommittee “Latest trends in elemental technologies supporting motion control – Gears and their rivals”, Kanagawa Prefecture, January 2020. |
7 Deliverables related to subsidized projects
(1) Nothing created through the subsidized project
(2) Anything created under this project other than (1) Publication papers mentioned above, etc.
8. Contact for inquiries regarding business details
Affiliated institution name: Tokyo Institute of Technology
Address: 2-12-1 (i6-15) Ookayama, Meguro-ku, Tokyo 152-8552
Applicant: Associate Professor Yusuke Sugahara
Department in charge: School of Engineering, Department of Mechanical Engineering, Department of Functional Systems
E-mail: info[at]msd.mech.e.titech.ac.jp ([at]→@)
URL: http://www. msd.mech.e.titech.ac.jp/