*This page contains summary public relations materials for the 2021 research grant from JKA Public Interest Incorporated Foundation, “Research on an interconnected structure-variable cable robot system using a reticular cableway self-propelled machine and a throwing/thrown machine.”
1 Overview of the research
In this research subsidy project, we will expand the concepts of a reticular cableway self-propelled robot and a structurally variable wire robot that were proposed and developed under research subsidy in FY2017/2019, FY2019/2020. We propose a distributed and interconnected structure-variable cable robot system consisting of a throwing robot that constructs a cableway in the environment, and a thrown robot that is thrown while towing the cable, and study the mechanism and control of the self-propelled machine, the cableway generation method, We conducted research to develop elemental technologies such as throwing robots, thrown robots, cooperative motion generation and control methods, and their frameworks.
2 Purpose and background of the research
In the FY2017 research subsidy project (multi-year), the research representatives used cables (called reticular cableway), which are interconnected like a spider’s web and constructed in a spatial and curved manner, as a track. We proposed a self-propelled robot that runs on a mesh cableway. In addition, we proposed a structure-variable series/parallel hybrid parallel wire robot that uses multiple cables to drive hand effectors using multiple cables fed out from the robot. We have been developing practical technology.
The new problem here is how to construct a cableway in the environment. Up until now, it has been assumed that workers manually erect cables and construct reticular cableways, but since it is assumed that workers manually install cables and construct reticular cableways, it is difficult for humans to approach. It was impossible to operate the system in environments where it was not easy to do so. If robots can build this automatically, they will be able to operate in environments that are difficult for humans to approach.
Therefore, in this study, we propose a distributed reconfigurable robot system interconnected by cables, which is an extension of the concepts of these reticular cableway self-propelled robots and variable-structure wire robots. In addition to the self-propelled network cableway robot, this system consists of a throwing robot that constructs a cableway in the environment by throwing cables, and a thrown robot that is thrown while towing the cable.These robots are used to automatically construct a network cableway in an unmaintained environment. It is a field robot system that can self-propel above the tower and position itself below the cableway by descending from there.
The purpose of this research was to develop elemental technologies and their frameworks, such as the mechanism and control of self-propelled machines, cableway generation methods, throwing robots, thrown robots, and cooperative motion generation and control methods.
3 Research content
The plan for this research is divided into multiple research items, and the implementation details for each item are shown below.
①Optimized design of self-propelled mesh cableway machine
For operational research in an actual outdoor environment, which began with this research, we designed a reticular cableway self-propelled vehicle that achieves high maneuverability and reliability (Figures 1 and 2). We have also started operational experiments to use it for ecological surveys of wild animals. This experiment was conducted in July 2022 on Rishiri Island, Hokkaido, as part of a black-tailed gull ecology survey conducted by Waseda University’s Wildlife Ecology Laboratory, Faculty of Human Sciences (Associate Professor Kentaro Kazama). I succeeded in photographing a baby black-tailed black-tailed black-tailed cat while running parallel to it at a distance of about 50 cm. The operating noise of the robot was low, and the black-tailed black-tailed cat did not appear to be alarmed (Video 1).
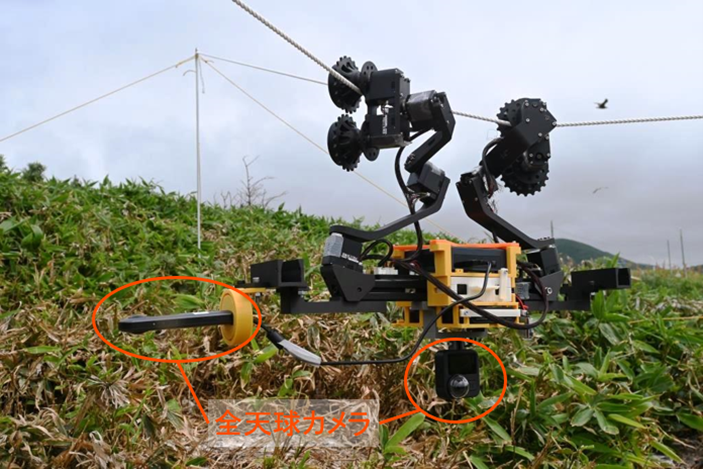
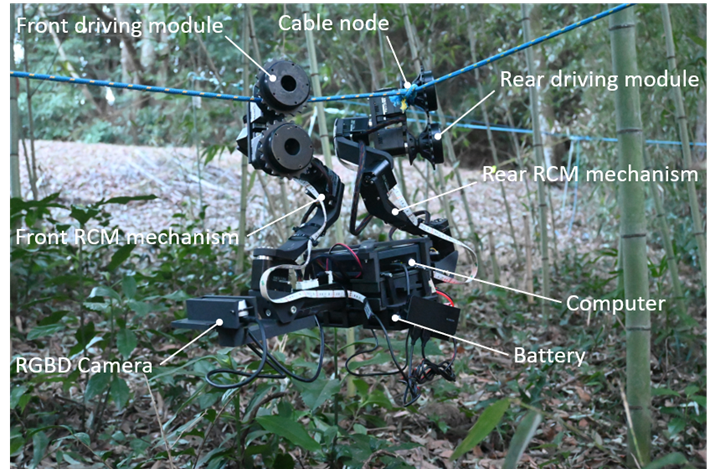
Video 1: TCC80DR: Wildlife monitoring experiment at black-tailed gull colony in Rishiri Island, Hokkaido.
②Development of a method for generating reticulated cableways
In order to operate a self-propelled robot (reticular cableway self-propelled machine) that runs on a spatially constructed cableway with interconnected cables in a new environment, it is necessary to determine the location of the start point and goal point in space, Based on the location and size of the obstacles, it is necessary to decide how to stretch the network cableway so that the self-propelled aircraft can complete the route. Here, after generating multiple route candidates using Q-RRT*, we find the cable tensioning method that achieves each route, and then derive the tension and cable deformation during running based on an elastic catenary model. We developed a method to find a network cableway that a self-propelled vehicle can complete, and then select the optimal solution based on the time it takes to overcome knots and the total distance of the route.
The validity of this method was verified through experiments and simulations. Figure 3 shows an example of the calculation results for the main rope and sub-route when there are two obstacles, and the representative points of a running self-propelled aircraft, and Video 2 shows an experiment in which the cableway was actually run.
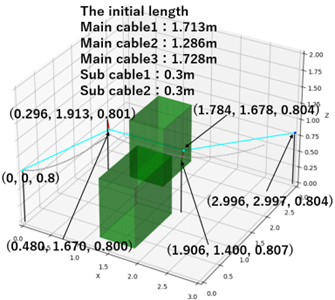
Video 2: TCC80DRII: Spatially Structured Cableway Planning Method Taking Cable Deformation into Consideration.
③ Research and development of cable throwing robot
In this research and development project, we worked on constructing a mathematical model of cable throwing, controlling the throwing motion based on the model, and prototyping a cable throwing robot experimental device in order to autonomously realize cable-throwing and other tasks using robots. In modeling, various parameters in the conventionally constructed model were identified based on experimental results, and their validity was confirmed. Furthermore, using the mathematical model, we developed a robot control method to achieve throwing using nonlinear control. Specifically, input/output linearization and output zero control are used. Furthermore, in order to confirm the effectiveness of these models and control methods, we proceeded with the development of a three-degree-of-freedom planar serial link manipulator with flexible nodes.
Video 3 shows an example of the calculation results of the throwing motion using the manipulator.
Video 3: Motion of fly-fishing.
④ Research and development of cable-pulling/throwing robots
In this research and development item, we will solve the problem of how to fix the cable end to some object in the environment, which is a problem when constructing a cableway by throwing a cable, by using a throwing robot that can be attached to the end of the cable. I tried. Specifically, we developed a small throwing robot equipped with a mechanism that allows multiple claws to be opened and closed by wireless control to grip uneven surfaces of objects.
Video 4 shows the experiment with the thrown robot.
Video 4: Experiment with a thrown robot.
⑤Cableway measurement and control method for reticular cableway self-propelled robot
In order to make the reticular cableway self-propelled machine run autonomously, it recognizes the location of the branch point and the angle of the cableway without using visible light, autonomously plans operations that will not run off the cableway, and reaches the branch point at a stable speed. We have developed a control method that passes through. First, we developed a method to apply tension to the cableway to obtain sufficient frictional force and to plan a target trajectory for passing through junctions that is unlikely to run off. Next, we developed an algorithm to estimate the location of the branch point and the angle of the cableway using IMU and depth images. Furthermore, we developed an algorithm that estimates the traveling speed of a self-propelled aircraft from the temporal changes in these parameters and determines the timing to start the operation of passing through a junction.
Videos 5 to 7 show an experiment in which a networked cableway with multiple branch points was constructed outdoors. Video 5 shows the vehicle running under sunlight during the day, Video 6 shows the vehicle running at night with floodlights on, and Video 7 shows the vehicle running at night without any lights. Both machines operated continuously for 15 minutes without misrecognizing any branch points, and succeeded in passing through the branch points 14 times. Video 8 shows the Depth camera image at this time. The system was able to recognize branch points without any problems even in situations where trees were reflected behind the branch point.
Video 5: TCC80DRII: Cable nodes recognition and automatic driving under sunlight.
Video 6: TCC80DRII: Cable nodes recognition and automatic driving at night under lighting.
Video 7: TCC80DRII: Cable nodes recognition without visible light and automatic driving at night.
Video 8: TCC80DRII: Cable nodes recognition using onboard depth camera.
Videos 9 to 12 show similar experiments conducted in the forest on Waseda University’s Tokorozawa campus. It was possible to automatically recognize junctions and continue driving both in the middle and at night.
Video 9: TCC80DRII: Cable node recognition and automatic driving in natural forest.
Video 10: TCC80DRII: Cable node recognition and automatic driving in natural forest.
Video 11: TCC80DRII: Cable node recognition and automatic driving in natural forest.
Video 12: TCC80DRII: Cable node recognition and automatic driving in natural forest.
Furthermore, regarding the operation plan for passing through a branch point, we focused on the fact that the path of the drive section was traditionally modeled as two straight lines, but in reality the drive section travels on a curved path, and We have developed a method to generate a curved route by combining the route taken when the cable runs while the groove is fitted into the cable, and the route taken when the cable runs while deviating from the groove. We also developed a method to determine the position and orientation of one of the front and rear drive units from the position and orientation of the other. By combining these, the front and rear drive parts can now follow a curved trajectory while satisfying mechanical constraints, making it possible to smoothly pass through junctions without stopping the drive wheels.
Video 13: TCC80DRII: Nonstop node passage motion.
⑥ Expansion of generation method for reticular cableway ⑦ Cooperative reconfiguration motion generation and control method
We expanded the generation method of reticulated cableways and developed an automatic cable tying device to automatically construct reticulated cableways, including expansion of reticulated cableways by throwing and lowering. First, we designed and produced a manual principle verification model for generating secondary ropes by creating a stop knot (single knot) for the main rope, and confirmed that it was possible to create a stop knot for the main rope. Next, we designed and manufactured an electric automatic bundling device for automatically bundling cables, and verified its operation.
Video 14: Cable bundling principle verification: Single knot (double speed).
⑧Advanced research and development items
As an advanced research and development item, we prototyped and investigated three types of elemental technologies related to cable-throwing robots with different principles. In particular, we devised the principle of an anchor that can be attached to and detached from the environment by controlling the tension of the cable, and experimentally investigated its basic functions through simulations and experiments.
4 How this research will be utilized in the real world – Outlook
In the medium to long term, the results of this research are expected to lead to the realization of highly efficient, fast, and reliable mobile robots that are useful for continuous transportation of supplies and patrols in undeveloped environments such as mountains and disaster sites. This innovation is the realization of a high-power mobile robot that is useful for investigation, rescue, and work in natural environments with many obstacles, disaster sites, etc. These technologies can be applied to disaster response robots, decommissioning robots, decontamination robots, natural environment monitoring robots, and agricultural and forestry robots, and the results of this research are essential for the practical application of these robot systems. be.
Based on the results of this research, we have further expanded the theme to formulate a research plan entitled “Research on variable structure and deployable cable robot system with multiple robots interconnected,” and will receive research support (multi-year research) in 2023-2024. I applied, received a grant, and have begun research. This is an expansion of the concept based on the results of this research, and consists of multiple self-propelled machines, throwing machines, thrown machines, and automatic cable tying machines. We are planning to propose a reconfigurable-deployable cable-interconnected multi-robot system that can deploy a cableway structure by bundling and attaching it, and use it to perform positioning. We hope to see further results.
Regarding practical application, we are continuing to conduct operational experiments for monitoring wild animals, and we have received offers from companies for applied research in multiple fields, so we believe that we can expect early practical application.
5 Positioning of this research in the flow of teaching and research history
Yusuke Sugawara, the principal investigator, has made it his life’s work to build and develop robot system design, and among these, the “reticular cableway self-propelled robot” and “structure-variable hybrid wire mechanism” are proposals for completely new robot systems. This is of great significance in the sense that it is carried out. In addition, the concept of applying a parallel wire mechanism to a self-propelled working mobile robot on an orbit is a challenge for me as a mechanism researcher, especially in the field of field robotics, which has been rapidly developing recently, such as drones and SLAM.
Co-researcher Hiroshi Endo has been working on the application of robot technology with sustainability as a keyword in his past research, and this research, which can be applied to monitoring lakes and forests, is positioned in that direction. We are also working on research on parallel wire mechanisms focusing on the characteristics of wires and on systems using mobile robots, which are important as applied research for these basic technologies.
Co-researcher Hiroyuki Ishii is working on the development of robot technology that coexists with nature and living things, and in recent years has particularly focused on developing robots for observing and preserving wild animals and plants in forests. The reticular cableway self-propelled robot being developed in this research is extremely promising as a new movement technology in forests, and is also expected to collaborate with the environmental monitoring robots that have been developed so far, making it possible to use robots to monitor forests. It is positioned as an important and rapidly accelerating research.
Research collaborator Jun Kinugawa has been researching calibration methods and control methods for parallel wire drive devices, and in recent years has been working on applying them to the development of robot technology to protect the rich forests of Fukushima Prefecture. The mesh cableway self-propelled robot being developed in this research has high expectations for its use in forest maintenance, and is positioned as an important research for the conservation of the natural environment using robot technology.
6 Intellectual property, published papers, etc. related to this research
【Research Articles】
1. | Yusuke Sugahara, Taishu Ueki, Daisuke Matsuura, Yukio Takeda and Minoru Yoshida, Offline Reference Trajectory Shaping for a Cable-Driven Earthquake Simulator Based on a Viscoelastic Cable Model, IEEE Robotics and Automation Letters, Vol. 7, No. 2, pp. 2415-2422, April 2022. |
2. | Hirotsugu Kano, Yusuke Sugawara, Osamu Endo, Hiroyuki Ishii, Yukio Takeda, Research on robots that run by themselves on a net-like cableway constructed structurally in space – On the kinematics of double-arm type, motion planning and mechanism optimization ―, Journal of the Robotics Society of Japan, Vol. 39, No. 8, pp. 767-770, October 2021. |
[International conference (peer-reviewed)]
3. | Kazuki Hayashi, Yusuke Sugahara, and Yukio Takeda, Experimental Study on Thrustered Cable-Suspended Parallel Robot for Collaborative Task, Proceeding of the 6th International Conference on Cable-Driven Parallel Robots (CableCon2023), Nantes, France, June 2023.(印刷中) |
4. | Andres Osorio Salazar, Yusuke Sugahara and Yukio Takeda, A Differential Mechanism to Enhance the Scalability of a SMA-Wire-Bundle Linear Actuator, The 6th IFToMM Asian Mechanisms and Machine Science Conference (AsianMMS2021), Hanoi, Vietnum, Dec. 2021. In: Khang N.V., Hoang N.Q., Ceccarelli M. (eds) Advances in Asian Mechanism and Machine Science. ASIAN MMS 2021. Mechanisms and Machine Science, vol 113. Springer, Cham. |
[International conference proceedings (no peer review)]
5. | Ryosuke Hakamata, Mitsuru Endo, Yusuke Sugahara, Yukio Takeda, and Hiroyuki Ishii, Dynamic modeling and parameter identification of an elastic rod for analyzing fly-fishing, Proceeings of the 5th Jc-IFToMM International Symposium, 京都府,2022年7月.(A Finalist for Young Investigator Fund Best Paper Award) |
[Domestic conference proceedings]
6. | Yasunari Akimoto, Jun Kinugawa, Osamu Endo, Yusuke Sugawara, Prototype of a cable tying device for constructing a sub-cable starting point for a self-propelled reticulated cableway robot, Japan Society of Mechanical Engineers Robotics and Mechatronics Conference 2023, Aichi Prefecture, 2023. (currently printing) |
7. | Ryonori Hakamada, Osamu Endo, Yusuke Sugawara, Research on throwing with a small low-power manipulator applying fly fishing principles (generation of manipulator joint trajectory using nonlinear control), Japan Society of Mechanical Engineers Robotics and Mechatronics Conference 2023, Aichi Prefecture , 2023. (currently printing) |
8. | Atsuhiro Ichijo, Seiaki Baba, Ryonori Hakamada, Yusuke Sugawara, Osamu Endo, Hiroyuki Ishii, Kotaro Hoshiba, Yukio Takeda, Research on a robot that runs on a mesh cableway by itself (Development of a mesh cableway design method that takes into account cable deformation) ), 23rd Society of Instrument and Control Engineers System Integration Division Conference (SI2022), pp. 532-537, Chiba Prefecture, December 2022. |
9. | Wataru Matsuhiro, Takumi Iwabuchi, Kazuya Sumita, Ryota Nagai, Nu NuWin, Yusuke Sugawara, Junichi Haruyama, Hiroyuki Ishii, Atsuo Takanishi. Acquisition of running motion by reinforcement learning in a lunar vertical hole exploration robot using drop-shaped eccentric wheels , 66th Space Science and Technology Union Conference, 4A03, Nov. 2022. |
10. | Wataru Matsuhiro, Keita Noda, Ryota Nagai, Nu NuWin, Junichi Haruyama, Yusuke Sugawara, Hiroyuki Ishii, Atsuo Takanishi, Development of a small robot for exploration of vertical holes on the moon ~ Pendulum using a winch in a non-ground suspended state Control of motion, 40th Annual Conference of the Robotics Society of Japan, 3J2-03, Tokyo, September 2022. |
11. | Yoshihiro Wu, Keitaro Ishibashi, Yusuke Sugawara, Hiroyuki Ishii, Development of a wall-mounted robot using adhesive resin and claws – Prototyping and evaluation of claw parts combining soft and hard materials -, Japan Society of Mechanical Engineers Robotics and Mechatronics Conference 2022 , 2P1-M04, Hokkaido, June 2022. |
12. | Hoshiaki Baba, Yusuke Sugawara, Osamu Endo, Hiroyuki Ishii, Yukio Takeda, Development of a robot that moves by throwing and winding multiple tethers and suspending them (first report, concept proposal and experimental basic functions) Review), 22nd Society of Instrument and Control Engineers System Integration Division Conference (SI2021), pp. 607-612, Online, December 2021. |
13. | Wataru Matsuhiro, Shigehide Suzuki, Ryota Nagai, Keita Noda, Nu NuWin, Yusuke Sugawara, Junichi Haruyama, Atsuo Takanishi, Hiroyuki Ishii, Research on a small robot that explores vertical holes on the moon by wall jumping, 65th Space Science and Technology Union Lecture, 3K17, November 2021. |
14. | Ryota Nagai, Wataru Matsuhiro, NuNuwin, Shigehide Suzuki, Keita Noda, Yusuke Sugawara, Junichi Haruyama, Atsuo Takanishi, Hiroyuki Ishii, Impact resistance of a small robot that uses a winch and eccentric wheels to explore the wall of a lunar shaft Research on improvement of performance, 39th Academic Conference of the Robotics Society of Japan, 1D1-01, September 2021. |
15. | Ryonori Hakamada, Osamu Endo, Yusuke Sugawara, Hiroyuki Ishii, Yukio Takeda, Research on casting using a small, low-power manipulator applying principles of fly fishing (first report, modeling of line taking into account payout from the rod), Japan Japan Society of Mechanical Engineers Robotics and Mechatronics Conference 2021, 2P3-H15, June 2021. |
[Invited lectures, etc.]
16. | Yusuke Sugawara, Development of a new space-moving robot “reticulated cableway self-propelled robot” to replace drones, Ota Industrial Promotion Association 108th Tokyo Institute of Technology Technical Seminar, Tokyo, March 2023. |
17. | Yusuke Sugawara, Self-propelled cableway robot, Fukushima University Lecture “Robot technology to make Fukushima Prefecture’s rich forests sustainable”, Fukushima Prefecture, March 2023. |
18. | Osamu Endo, Robot technology to make Fukushima prefecture’s rich forests sustainable, Fukushima University lecture “Robot technology to make Fukushima prefecture’s rich forests sustainable”, Fukushima Prefecture, 2023 March. |
19. | Hiroyuki Ishii, Coexistence of nature, animals, and humans using robotics, Fukushima University Lecture “Robotic technology to make Fukushima Prefecture’s rich forests sustainable”, Fukushima Prefecture, March 2023. |
20. | Yusuke Sugawara, Reticulated cableway self-propelled robot, Japan Society of Mechanical Engineers 2022 Annual Conference Elemental Lubrication Design Division Planning Advanced Technology Forum “Fundamentals and Practical Application of Cable/Wire Driven Robots”, F113-03, Toyama Prefecture, September 2022 .. |
7 Deliverables related to subsidized projects
(1) Nothing created through the subsidized project
(2) Anything created under this project other than
(1) Publication papers mentioned above, etc.
8. Contact for inquiries regarding business details
Affiliated institution name: Tokyo Institute of Technology
Address: 2-12-1 (i6-15) Ookayama, Meguro-ku, Tokyo 152-8552
Applicant: Associate Professor Yusuke Sugahara
Department in charge: School of Engineering, Department of Mechanical Engineering, Department of Functional Systems
E-mail: info[at]msd.mech.e.titech.ac.jp ([at]→@)
URL: http://www. msd.mech.e.titech.ac.jp/jp/